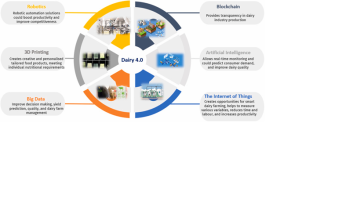
Smart Dairy Factory: Dairy.4.0 By: Vivekanand Nalla
Industry 4.0 creates a "smart factory" within which the Cyber Physical approach supervise physical processes, create a virtual copy of the physical world, and make reorganized decisions. Over the Internet of Things, cyber-physical systems communicate and assist with each other and with individuals in true time. The smart factory is a model used to define the application of distinct combinations of modern technologies to create a hyper-flexible, self-adapting manufacturing competence. And visibility, connectivity, and autonomy. Factories have long relied on automation, but smart factories take this concept much further and are able to run without much human intervention. The smart factory model is more efficient than old-style manufacturing because all processes are optimally associated. Production costs are lower, due in part to reduced downtime and less waste. Underutilized production capacity can be identified and removed. It is more specific concept that refers to a factory that utilizes Industry 4.0 technologies to enhance its manufacturing processes. Global wide many manufacturing companies are facing numerous challenges. They need to increase productivity while producing individualized offerings with high quality in a continually, as per changing environment trends and customer demand and sourcing complexities. Competition and cost strains to force many companies to continually optimize business operations to stay profitable. The world economy is on the jump of rapid digital transformation, and that it includes food processing. Technological advancements such as artificial intelligence, e-mobility, autonomous driving, and hyper-automation make digitization a necessity. Because the food industry involves many human elements and is both the driver and the subject of environmental impacts, adapting to 5.0 will be essential for rapidly changing innovation landscapes, the demands of society, and challenges such as pressure on natural resources, ecosystems, global warming, and population increase. Implementation of a robust innovation plan can begin with identification of the technologies suitable for specific food products and processes and consideration of industrial paradigm shifts for all-inclusive value chains. Industrial automation, Internet of Things (IoT) technologies, such as sensors, simulations, artificial intelligence based autonomous systems, cloud systems, and blockchain, are projected to have the greatest impact on the food processing industry by enabling integration of physical processes, computation, and networking in cyber physical systems. Systems of connected sensors, devices, machinery, and data analytics are helping businesses of various sizes improve efficiency, quality, and safety while reducing costs and timely service to market.
Such digitalization and integration can offer an unprecedented opportunity for business gains. Enabling technologies are under rapid development and their transfer to the food industry will be key. However, it will also be important to create resilient innovation pathways with human-inclusive strategies that consider human health, consumer preferences, and workforce model shifts. Food processing processes have benefited from Industry 4.0 concepts by improving traceability, monitoring, and control of food quality; improving safety, manufacturing, automation, and training; predicting sensory and consumer preferences; and reducing loss and waste. Antiquity of automation in industry 4.0, and Chronological perspective of Industry 4.0:
Steam to Sensor setup towards smart factory:
First industrial revolution: Starting in the late 18th century in Britain, the first industrial revolution helped enable mass production by using water and steam power instead of purely human and animal power. Complete goods were built with machines rather than meticulously produced by hand.
Second industrial revolution: A century later, the second industrial revolution introduced assembly lines and the use of oil, gas, and electric power. These new power sources, along with more advanced communications via telephone and telegraph, brought mass production and some degree of automation to manufacturing processes.
Third industrial revolution: The third industrial revolution, which began in the middle of the 20th century, added computers, advanced telecommunications and data analysis to manufacturing processes. The digitization of factories began by embedding programmable logic controllers (PLCs) into machinery to help automate some processes and collect and share data.
Fourth industrial revolution: We are now in the fourth industrial revolution, also referred to as Industry 4.0. Characterized by increasing automation and the services of smart machines and smart factories, informed data helps to produce goods more efficiently and productively across the value chain. Tractability is improved so that manufacturers can better meet customer demands using mass customization—ultimately seeking to achieve efficiency with, in many cases, a lot size of one. By gathering more data from the factory floor and combining that with other enterprise operational data, a smart factory can achieve information transparency and healthier decisions.
“The fourth industrial revolution” was first publicized in 2011 by a German manufacturing industry idea that aimed to increase the effectiveness of the national technological approach. The now globally adopted term refers to meeting the requirements of businesses and industrial products while also upgrading intelligence from cradle to cradle, through a complete combination of technology. As a result, two advances are made possible: extreme improvement in the effectiveness among supply chain members as well as at the interface of human and physical systems.
Industry 4.0 is a term that refers to the integration of digital technologies, such as artificial intelligence, robotics, internet of things, cloud computing, and big data analytics, into the manufacturing sector. Industry 4.0 aims to improve efficiency, quality, safety, flexibility, and innovation in production processes.
Industry 4.0 is a tactical urgency to turn these challenges into opportunities designing visible business outcomes leading to increased productivity, revenues, and value:
• Intensified ability to deliver on customer demand and expectations.
• Expanded productivity of assets and people
• Higher agility and visibility to respond to changing environments.
• Advanced time-to-market and agility for customization of products
• Environmental operations meeting societal demands.
• New revenue streams through business model innovations
• Exposure of industry specific needs, for example, segment of one for industrial machinery and component or compliance to regulations for pharma companies
• Extreme visibility across logistics operations with condition and status tracking Industry 4.0 is an intricate Cyber Physical approach: Internet of Things (IoT): The Internet of Things (IoT) is a key component of smart factories. Machines on the factory floor are equipped with sensors that feature an IP address that allows the machines to connect with other web-enabled devices. This system connects devices through a network, allowing the exchange of data. IoT has the potential to create intelligent environments with powerful tools in many agriculture and livestock areas, enabling the creation, modification, and sharing of information. IoT is increasingly being used in dairy farms to collect live, accurate data and share it with the farmer or other stakeholders. This mechanization and connectivity make it possible for large amounts of valuable data to be collected, analysed, and exchanged.
IoT in Dairy 4.0 approach:
• IoT can help dairy farmers monitor the health and well-being of their cows by using sensors, RFID tags, cameras, and smart collars that can track their temperature, heart rate, activity, milk yield, and location.
• IoT can help dairy farmers optimize their milking process by using automated milking systems, robotic arms, and smart sensors that can measure the milk quantity, quality, and composition.
• IoT can help dairy farmers reduce their environmental impact by using smart irrigation systems, soil sensors, weather stations, and drones that can measure the water usage, soil moisture, crop growth, and fertilizer needs. Big Data (BD): BD refers to extremely large and complex data sets that cannot be analysed or processed using traditional methods. Big Data Analytics (BDA) is the process of using advanced analytical tools and techniques to process these massive data sets. In the dairy industry, BD/BDA can be applied in several ways, as the dairy industry generates huge amounts of data. Applications relate to milk production, milk quality, farm management, real-time monitoring and decision-making, animal health, and supply chain sustainability.
Big Data in Dairy 4.0 approach:
• BD/BDA can help improve the milk quality by using sensors, cameras, and smart devices that can monitor the temperature, pH, fat, protein, and somatic cell count of the milk at various stages of production, processing, and distribution.
• BD/BDA can help ensure the traceability of the dairy products by using RFID tags, QR codes, blockchain, and cloud computing that can record and store the information about the origin, location, movement, and status of the dairy products throughout the supply chain.
• BD/BDA can help increase the efficiency of the dairy products by using predictive analytics, machine learning, and optimization algorithms that can forecast the demand, supply, and price of the dairy products and adjust the production, inventory, and distribution accordingly. Cloud computing: Cloud computing is a cornerstone of any Industry 4.0 strategy. Full realization of smart manufacturing demands connectivity and integration of engineering, supply chain, production, sales and distribution, and service. Cloud helps make that possible. In addition, the typically large amount of data being stored and analysed can be processed more efficiently and cost-effectively with cloud. Cloud computing can also reduce startup costs for small- and medium-sized manufacturers who can right-size their needs and scale as their business grows. AI and machine learning: AI and machine learning allow manufacturing companies to take full advantage of the volume of information generated not just on the factory floor but across their business units and even from partners and third-party sources. AI and machine learning can create insights that provide visibility, predictability, and automation of operations and business processes. For instance, industrial machines are prone to breaking down during the production process. AI is a computational technology used to mimic human abilities to perceive their environment, learn, and make decisions. In the food sector, AI techniques play a key role in automation in the smart farming and food processing industries and could help accelerate the transition towards sustainable food systems. Generally, AI-based technologies can be used in real-time monitoring and decision-making processes. Using data collected from these assets can help businesses perform predictive maintenance based on machine learning algorithms, resulting in more uptime and higher efficiency.
AI models in Dairy 4.0 approach:
• AI can help farmers optimize their crop yields by using sensors, drones, satellites, and weather data to monitor soil conditions, plant health, pest infestation, and irrigation needs.
• AI can help food processors reduce food waste by using computer vision, spectroscopy, and machine learning to detect defects, contaminants, and spoilage in raw materials and finished products.
• AI can help consumers make informed choices by using natural language processing, chatbots, and recommended systems to provide personalized nutrition advice, recipes, and product recommendations. Edge computing: The demands of real-time production operations mean that some data analysis must be done at the “edge”—that is, where the data is created. This minimizes latency time from when data is produced to when a response is required. For instance, the detection of a safety or quality issue may require near-real-time action with the equipment. The time needed to send data to the enterprise cloud and then back to the factory floor may be too lengthy and depends on the reliability of the network. Using edge computing also means that data stays near its source, reducing security risks. Cyber security: Manufacturing companies have not always considered the importance of cyber security or cyber-physical systems. However, the same connectivity of operational equipment in the factory or field (OT) that enables more efficient manufacturing processes also exposes new entry paths for malicious attacks and malware. When undergoing a digital transformation to Industry 4.0, it is essential to consider a cyber security approach that encompasses IT and OT equipment. Digital twin: The digital transformation offered by Industry 4.0 has allowed manufacturers to create digital twins that are virtual replicas of processes, production lines, factories, and supply chains. A digital twin is created by pulling data from IoT sensors, devices, PLCs, and other objects connected to the internet. Manufacturers can use digital twins to help increase productivity, improve workflows, and design new products. By simulating a production process, for example, manufacturers can test changes to the process to find ways to minimize downtime or improve capacity. Features of a smart factory approach: Data analysis for optimal decision making. Embedded sensors and interconnected machinery produce a significant amount of big data for manufacturing companies. Data analytics can help manufacturers investigate historical trends, identify patterns, and make better decisions. Smart factories can also use data from other parts of the organization and their extended ecosystem of suppliers and distributors to create deeper insights. By looking at data from human resources, sales or warehousing, manufacturers can make production decisions based on sales margins and personnel. A complete digital representation of operations can be created as a "digital twin." IT-OT integration: The smart factory’s network architecture depends on inter connectivity. Real-time data collected from sensors, devices and machines on the factory floor can be consumed and used immediately by other factory assets, as well as shared across other components in the enterprise software stack, including enterprise resource planning (ERP) and other business management software. Business manufacturing: Smart factories can produce customized goods that meet individual customers’ needs more cost-effectively. In fact, in many industry segments, manufacturers wish to achieve a "lot size of one" in an economical way. By using advanced simulation software applications, new materials, and technologies such as 3-D printing, manufacturers can easily produce small batches of specialized items for customers. Whereas the first industrial revolution was about mass production, Industry 4.0 is about build customization. Supply chain: Industrial operations are dependent on a transparent, efficient supply chain, which must be integrated with production operations as part of a robust Industry 4.0 strategy. This renovates the way manufacturers resource their raw materials and deliver their finished products. By distributing some production data with suppliers, manufacturers can better schedule deliveries. If, for example, an assembly line is experiencing a interruption, deliveries can be rerouted or delayed reducing wasted time or cost. Additionally, by examining weather, transportation partner and retailer data, companies can use predictive shipping to send finished goods at just the right time to meet consumer demand. Blockchain is emerging as a key technology to enable transparency in supply chains.
Industry 4.0 and hybrid multi cloud IT architecture Building: A hybrid multi cloud IT infrastructure is a key component in digital transformation for manufacturers seeking to take advantage of Industry 4.0. Hybrid multi cloud is when a company has two or more public and private clouds to manage their computing workloads. This gives them the ability to optimize their workloads across all their clouds, as some environments are better suited to or more cost-effective for certain workloads. Manufacturers looking for digital transformation and a secure, open environment can move their existing workloads from their on-premises location to the best possible cloud environment. Robotics – Robotics is an interdisciplinary and multidisciplinary field that combines advanced systems related to mechanical, electrical and electronics hardware and software. The use of robotics in the food industry can vary between simple repetitive tasks to complex processes. Robotics technology has been long in use in many manufacturing sectors, e.g., automotive, but potential applications for robotics in dairy industries is being investigated. 3D Printing: Ideas for 3D Application Futuristic It creates food products with similar consistency and repetition with parameters such as shapes, size, and decoration, e.g., celebration cakes with artistic decoration. Creative It creates creative and personalized, specially textured food products to suit individual nutritional requirements without discomfort. Healthy It facilitates the accurate dispensing of ingredients and nutrients during the printing of food products. Efficient It allows layer-by-layer deposition during a process using the most efficient pathway. Sustainable It results in zero waste or minimal excess material being disposed of in the process and is therefore sustainable. Three-dimensional (3D) printing technology (or additive manufacturing) has emerged recently as a promising innovation that uses digital data to create various types of solid and semi-solid food products. Over the last few years, the application of 3D printing has gained enormous interest in many food sectors. There has been a rapid increase in scientific work focusing on the 3D printing of dairy products. Dairy products and ingredients contain of different constituents, functionalities, and structures, making them a very challenging but at the same time very favourable source of raw materials for 3D printing of food. 3D impact on Dairy 4.0 approach:
• 3D printing can overcome the challenge of maintaining the stability, texture, and flavour of dairy products by using appropriate printing parameters, such as temperature, pressure, speed, and nozzle size, that can control the rheological properties, thermal behaviour, and microstructure of the dairy materials. • 3D printing can utilize the potential of creating novel and complex shapes and structures of dairy products by using computer-aided design (CAD) software, digital models, and slicing algorithms that can generate the printing path and instructions for the printer.
• 3D printing can utilize the potential of enhancing the nutritional value and functionality of dairy products by using customized formulations, additives, and fortifications that can tailor the dairy products to specific dietary needs and preferences.
Themes 3D Application Futuristic It creates food products with similar consistency and repetition with parameters such as shapes, size, and decoration, e.g., celebration cakes artistic decoration. Creative It creates creative and personalised specially textured food products to suit individual nutritional requirements without discomfort. Healthy It facilitates the accurate dispensing of ingredients/nutrients during printing of food products. Efficient It allows layer-by-layer deposition during a process using the most efficient pathway. Sustainable It results in zero waste or minimal excess material being disposed of in the process and therefore sustainable.
Blockchain: Blockchain can be considered one of the industry 4.0 enablers and can address the growing industry need for considerably more reliable and efficient supply chain management infrastructure. Blockchain technology can be defined as cryptographically secured distributed ledgers where the ledgers are distributed in a peer-to-peer format among the entities, making it a decentralized system. There is a need for decentralized solutions such as blockchain due to the single points of failure, product irregularities, quality compromises, and loss of data present in conventional food supply chains. Adoption of blockchain in the food supply chain, especially when combined with other technologies such as IoT, enables data interoperability, cost reduction, transparency, audibility, integrity, and authenticity. To protect vulnerable populations, blockchain solutions that go beyond food traceability to maintain the nutritional values of dairy products and identify their adulteration and contamination have been proposed.
Block chain models for Dairy 4.0 approach:
• Blockchain and IoT can work together to create a digital identity for each dairy product by using smart tags, sensors, and QR codes that can store and transmit the information about the origin, location, movement, and status of the product throughout the supply chain.
• Blockchain and IoT can work together to create a smart contract for each dairy transaction by using smart devices, RFID readers, and bio metric scanners that can verify and execute the terms and conditions of the contract automatically and securely.
• Blockchain and IoT can work together to create a data-sharing platform for all the stakeholders in the dairy supply chain by using cloud computing, edge computing, and encryption techniques that can enable the data interoperability, transparency, auditability, integrity, and authenticity.
The “Dairy 4.0” concept, inspired by Industry 4.0, is introduced and its enabling technologies are determined. Second, relevant examples of the use of Dairy 4.0 technologies in milk and its derived products are presented. 1. applications of dairy 4.0 technologies in milk and dairy products 4.1. Robotics, later Robotics has been more recently embraced by the dairy sector, other several applications areas. For instance, automatic milking systems are one of the most successful applications of robotics in the dairy industry. This system allows for a substantial average increase in milking frequency and therefore increased milk production, while reducing labour costs. Further identified benefits of automatic milking systems are increased overall productivity, profitability. 2. Another application of robotics in dairy farms is on floor cleaning, which helps to mitigate risks regarding cow welfare and to avoid ammonia emissions. In addition, sensors placed in the robotic system allow accurate and live data to be collected.
These data can be used to predict the value of important parameters such as daily milk yield and milk composition. Dairy 4.0 is a term that refers to the application of Industry 4.0 concepts and technologies to the dairy industry. Dairy 4.0 can help dairy manufacturers optimize their operations, reduce costs and waste, improve food safety and quality, increase traceability and transparency, and meet customer expectations. Industry 4.0 prospects: • Industry 5.0: This is the next stage of industrial evolution, which aims to combine human intelligence and creativity with machine capabilities and efficiency.
Industry 5.0 will focus on human-machine collaboration, social responsibility, and customer experience. • Edge computing: This is a technology that enables data processing at the edge of the network, rather than in the cloud or a central server. Edge computing can improve latency, bandwidth, reliability, and security of industrial applications.
• Digital twins: These are virtual replicas of physical assets, processes, or systems that can be used for simulation, optimization, or prediction. Digital twins can help manufacturers improve their design, testing, monitoring, and maintenance of their products.
Industry 4.0 benefits:
• Industry 4.0 offers opportunities to save energy while improving energy productivity and may help manufacturers remain competitive in tight markets.
• Increased productivity and efficiency: By using AI and Big Data to analyse data from sensors, machines, and products, manufacturers can optimize their operations, reduce downtime, improve quality, and increase output.
• Enhanced flexibility and customization: By using robotics and automation to adapt to changing customer demands, manufacturers can offer more variety, personalization, and innovation in their products.
• Improved safety and sustainability: By using IoT and cloud computing to monitor and control the environmental impact of their activities, manufacturers can reduce energy consumption, waste generation, and greenhouse gas emissions.
• The resulting end-to-end transparency in the value-adding process is a major advantage of a smart factory: it can reduce lead times, reveal disruptions in the operating process, increase plannability and thus ensure increased productivity and lower costs.
• improved energy efficiency, optimized energy-use, and reduced carbon emissions
• increased production output and product improvements across the value chain
• improved plant reliability, better product quality and reduced maintenance costs
• increased deployment of onsite renewable energy in the manufacturing process
• better connectivity with customers and supply chains
• Greater flexibility to produce differentiated products.
• Enhanced workplace safety and labour utilisation.
Industry 4.0 Barriers:
• High investment costs: Implementing Industry 4.0 technologies requires significant capital expenditure, as well as skilled labor, infrastructure, and maintenance.
• Cyber security risks: Connecting industrial systems to the internet exposes them to potential cyber attacks, which can compromise data privacy, operational integrity, and safety.
• Social and ethical issues: Adopting Industry 4.0 technologies may have implications for the workforce, such as job displacement, skill gaps, and ethical dilemmas. Various Industry 4.0 in the dairy 4.0 approach:
• Proactive maintenance and optimization of production and logistical chains, such as robotic milking machines and processing and packaging line automation reinforced by sensors for rapid chemical and microbial analysis with improved and real-time data management.
• Digitization of the entire value chain, from farm to fork, by using weather forecasts, customer preferences, traceability systems, and market access platforms to improve efficiency, quality, and sustainability.
• Analytics and decision support tools that use data from sensors, machines, and products to optimize operations, reduce downtime, improve quality, and increase output. The results revealed that robotics, 3D printing, Artificial Intelligence, the Internet of Things, Big Data, and blockchain are the main enabling technologies of Dairy 4.0.
These advanced technologies are being progressively adopted in the dairy sector, from farm to table, making significant and profound changes in the production of milk, cheese, and other dairy products. It is expected that, soon, new digital innovations will emerge, and greater implementations of Dairy 4.0 technologies is likely to be achieved, leading to more automation and optimization of this dynamic food sector. Industry 4.0 technologies implementation in dairy industry requires a greater collaboration and coordination among supply chain stakeholders to ensure that new technologies are effectively integrated into existing systems.
Even while technology advancements and digitalization have the potential to be very beneficial for the dairy business, there are still several obstacles that must be overcome to fully realize these advantages. These include issues related to digital infrastructure and connectivity, the cost of implementing new technologies, the need for skilled labour, and the need for greater collaboration among supply chain actors. To take advantage of technological advancements and make sure that the dairy business is competitive and sustainable in the future, it will be essential to address these difficulties.